MEMS open the way to ultra-lightweight and low-cost x-ray optics
Grazing-incidence x-ray optics are widely used in biological diagnostics, nuclear physics, and space research. However, the usable grazing-incidence angle is small, less than several degrees at 1keV. Therefore, to collect photons from weak sources in x-ray astronomy, multiple mirrors with smooth surfaces, comparable to the x-ray wavelength, are prepared one by one. The number of mirrors ranges from a few to thousands; fabricating all these mirrors is costly and labor intensive and, as the number of mirrors increases, the telescope becomes heavy and more expensive to launch. To drastically decrease these fabrication and launching costs for future missions, new ideas are necessary.
How can we decrease the telescope weight? One solution is to shrink it. If we shrink the size of the mirrors in the telescope by a factor of A, the mirror weight decreases by A.1 To keep the same effective area, we have to increase the mirror number by A.2 Consequently, the telescope weight will decrease by A. This is the basic idea of so-called micro-pore optics. The limit of this size reduction comes from x-ray diffraction, which is determined by the x-ray energy and the distance between the mirrors.
Micro-pore optics have μm- to mm-scale through holes and use their side walls as x-ray mirrors. Our approach is to use the semiconductor micro-structure fabrication technologies (micro-electro-mechanical systems, or MEMS) for micro-pore optics. We use anisotropic wet etching and deep reactive ion etching (D-RIE) to obtain reflection planes and accurately defined optic shapes, respectively.1–3
Figure 1 illustrates the concept of MEMS x-ray optics. We etch silicon (110) wafers in KOH solution, to fabricate smooth silicon (111) planes vertical to the wafer face that we use as x-ray mirrors. Because the crystal plane is limited in a certain direction, we release mirrors from the wafer and arrange these mirror chips onto an optic mount manufactured by the D-RIE. The mount consists of through holes and step structures on which the mirror chips are placed. By stacking a pair of these optic mounts, an approximated Wolter type-I optic is realized.

MEMS x-ray optics have important advantages: mass fabrication of x-ray mirrors at very low cost, and an extremely light weight thanks to producible fine holes (several μm) and thin wafers (several hundreds of μm). The mirror surface roughness may be larger (several nm) than traditional mirrors (< 1nm), and this problem needs further study. Other problems that need to be addressed include difficulties related to the high aspect ratio (i.e., the ratio of hole size to the wafer depth), and degradation of angular resolution due to the collinear approximation of ideal Wolter type-I optics and misalignment of optic components.
In recent years, great progress has been made in developing MEMS x-ray optics, and reflection on silicon (111) planes has been detected for the first time.2,3 Also, the micro-scale roughness of the side walls has been improved from several nanometers to less than 1nm.1 The best aspect ratio has increased from 10 to 201 and further improvement is expected.
In order to establish the fabrication process for the optics and to evaluate its performance, a single-stage optic is under development. Figure 2 shows the fabricated mirror chip and the optic mount, the high geometrical accuracy of which allows for a small misalignment angle (on the order of arcminutes). The release of the mirror chip from the wafer needs some future work.
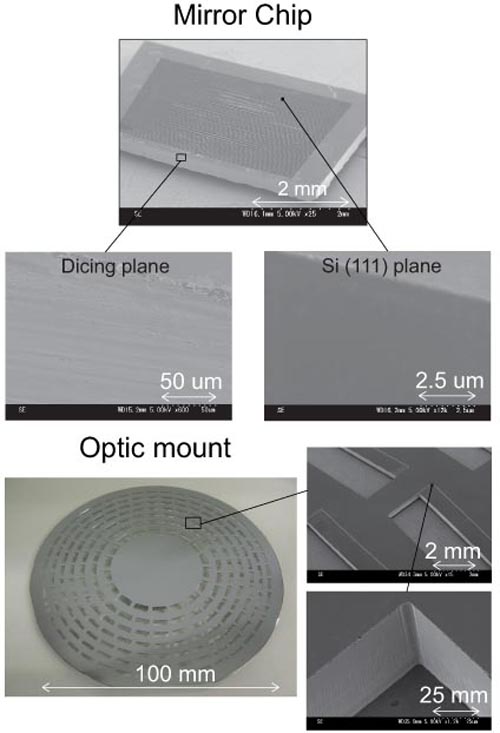
The expected performance of MEMS x-ray optics is shown in Figure 3. Because of its smaller pore size relative to those of micro-channel plate (∼20μm) and high-performance pore optics (∼200μm), MEMS can provide the lightest micro-pore optics. The angular resolution is limited by the collinear approximation, the misalignment, and the mirror flatness.
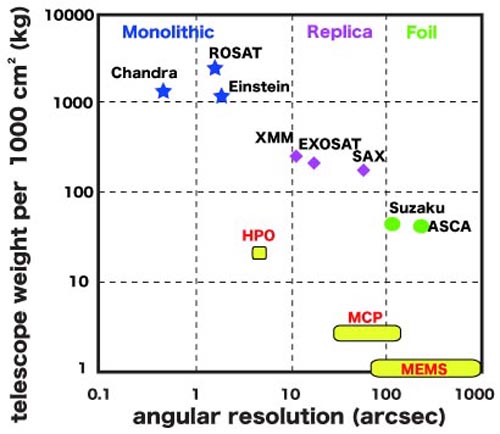
Further study is necessary before completing the manufacture of MEMS x-ray optics. Rapid progress suggests that it may be an option for future astronomical missions in which an extremely large effective area and/or a wide field of view with moderate angular resolution are necessary. Small satellite missions such as the Japanese mission DIOS4 should be favorable applications. The 1kg-class space x-ray telescope may be coming soon.
Yuichiro Ezoe, a JSPS postdoctoral fellow, earned his M.S. in optics and Ph.D. in astrophysics from University of Tokyo.
Masaki Koshiishi is a graduate student at ISAS/JAXA and University of Tokyo.
Kazuhisa Mitsuda is Director of High Energy Astrophysics department at ISAS/JAXA.